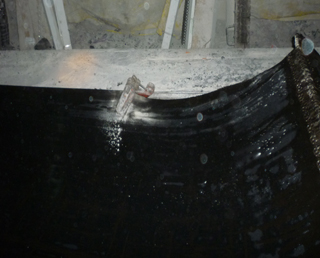 |
Edge clamps, while convenient, should not be used for clamping your belt. |
Maintenance ... it’s a fact of life when you are working with conveyors. And safe maintenance is of utmost importance on the job. While you can’t control all the variables that come with working in tough conditions – inclement weather, abrasive materials, etc. – you can control how you prepare your belt for safe repair. Workplace accidents are nothing to take lightly – they can cause worker injury and severely affect your productivity. In addition to locking out and tagging out your belt conveyor system and wearing proper PPE, clamping your belt properly is one of the most important steps you can take to avoid a catastrophic event.
When to clamp
Let me make this very clear … clamping the belt is a necessity every time you repair a belt. It doesn’t matter if you are 100 feet off the ground, or 100 feet underground, clamping is one of the most important safety precautions you can take during a repair. Whether you are pulling the belt ends together to install a splice, or going to work on your idlers, clamping the belt is the safest way to begin your repair.
Homemade vs. engineered belt clamps
Serious injuries are possible when clamping is done without using the proper tools and products. Oftentimes, people will use a c-clamp and lumber to hold their belt. While that may seem attractive for a quick fix, many things can go wrong. Lumber will bend easily, leading to only two points of contact with the belt. C-clamps are also prone to slipping, which may cause injury or a delay in repairs if the belt falls to the ground.
Engineered belt clamps are designed to work specifically with conveyor belts. Made with durable materials, they are more reliable than a piece of lumber that can easily snap under pressure. Trust me when I say, you don’t want to find out the hard way that using equipment not rated for your belt is a recipe for disaster.
Engineered belt clamps provide even tensioning across the entire belt width. They are also available in a variety of sizes so that you can choose the correct set for your belt conveyor system.
What kind of belt clamp do I need?
Hopefully, by now, I have you convinced to go with an engineered solution for your belt clamping needs. It’s important to know that there are many different styles of belt clamps out there, and they are used differently.
The first and most important thing to consider when choosing your belt clamps is the weight of the belt you are supporting. This depends on multiple factors such as conveyor layout and location of clamping. Once you know that, you will be able to choose from belt clamps that can handle your application. Remember to unload your belt to minimize extra load on the clamps.
A modular system is what you will want to look for next when selecting your belt clamps. Given the fact that you may be dragging them underground, up on a catwalk, or into tight spaces, you need to make sure they are mobile and easy to move. Most belt clamps are made with aluminum bars that are easy to transport.
Next, you will want to examine the grip pattern on prospective clamp bars – after all, the grip is the most important function of clamp bars. An extruded, non-slip grip or built-in grooves are your best choices for superior holding ability.
Finally, you will want to look at the type of belt you are repairing – flat, sidewall, chevron, etc. – as well as the width, to determine if the belt clamps you are interested in will work.
Types of clamping mechanisms
Belt clamps have different methods in which they actually clamp to your belt. Scissor clamps and over-the-belt clamp ends are two of the methods we will address in this blog. Scissor clamps, like Flexco’s FAR-PUL™ HD® Belt Clamps, are usually better for use with lower-load applications up top 3-tons which is common in aggregate. They accommodate a variety of belt widths belts up to 72" (1800 mm) wide and are constructed from heat-treated extruded aluminum to resist corrosion and prevent seizing in wet and corrosive environments.
Over the top belt clamps, like Flexco’s new TUG™ HD® Belt Clamps are designed to secure the belt by clamping over it for greater strength in higher-load applications rated from 6- to 8-tons, making them ideal for mining applications. The over-the-top grip also allows them to grip more of the belt, which is helpful for worn belts up to 96" (2400 mm) and sidewall belts. The acme thread on our new TUG belt clamps offers superior grip strength, but also allows operators the chance to slowly release the belt after maintenance. Check out our TUG HD Belt Clamp Installation Video for more information on our newest easy-to-use and transport belt clamps.
Inspect your clamps
Another safety measure we always recommend taking is inspecting your belt clamps when you initially receive them and before each use. You can never be too careful with a tool that could release your belt without warning, causing injuries to everyone in its path. Here are a few things to check when conducting your safety evaluation:
- The gripping surface on clamp bars: they should not be damaged in any way.
- Cracks on clamp bars, clamp ends or scissors: it only takes one crack to bust open a clamp bar, clamp end or scissor and send your belt flying.
- Bending and warping of clamp bars: again, this is something to take seriously as it affects the integrity of your hold.
- Scissor links or hardware damaged or missing pieces: do not operate clamps if the equipment is damaged or pieces are missing.
- Missing retaining pins: they are there to make sure the scissors remain secured on the bar. If they are missing, there is no guarantee your scissors won’t slip.
Along with your clamps, you will want to make sure your other tools are in good shape. Ensure you have the proper wrenches for tensioning your belt and that your come-alongs are in proper working order and not over-rated for the job.
Authored by: Aaron Rosso, Senior Product Manager
Rosso is responsible for managing the heavy-duty mechanical belt fastener program globally for Flexco, including the program vision and strategy, product development plan, product line portfolio, promotion, PR and communications, pricing, and profitability. Rosso graduated from Western Michigan University with a bachelor’s degree in Finance and received his master’s degree in business administration from the Kellogg School of Management at Northwestern University with a concentration in Marketing and Strategy.