I’ve seen a lot of things in my tenure here at Flexco. We’ve had some amazing product introductions, industry-changing product updates, and even some great advances in technology. But I have to admit that I always get a little excited when a custom order comes across my desk. Sometimes, they are simple tensioner changes and sometimes they are larger blades, but every once in a while, a special custom order comes through that makes you whip your head around and take notice.
Many people don’t know that if one of Flexco’s Belt Conveyor Products (BCPs) doesn’t fit your application, we offer our expertise and experience to help you find a solution. We’ll listen to your challenge, bounce the idea off our product and industry experts, and come back to you with a recommendation that resolves your issue.
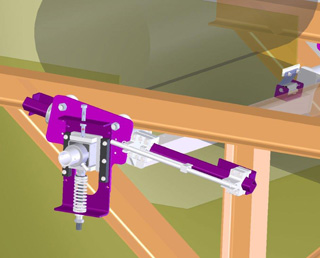 |
Here is a rendering of a retractable MHS cleaner that was installed in a Midwest iron ore mine. |
Sometimes it’s an easy fix like a longer pole or a different blade. We have even gotten into the habit of providing cleaners with pole offsets so they can be properly fitted into the application without field modification, making our customers (and our field service specialists) very happy. No more onsite welding to fix it – we can do it right in the shop and ship it to you for easy installation.
Tackling the Big Belts
And then there’s the BIG belts … the ones that no one knows what to do with or, more importantly, how to keep clean. Territory Manager Larry Tindle faced one of those just recently when he was brought in to spec a cleaner for a filter belt. Carryback was a huge problem for his customer and the homemade solution just wasn’t cutting it. The customer was wrapping wires around the head pulley and hooking them to the frame. It worked well, but the wires were thin and breaking and then their sharp ends were quite the hazard.
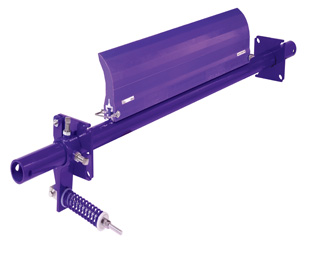 |
Standard EZP1 Precleaner. Our custom Flexco solution included two 60” blades on an extended pole. |
They were in search of something better that required less maintenance. Larry was sure that the Flexco EZP1 Precleaner would get the job done and he had a blade on hand to show them that it was tough enough to scrape off debris, but easy enough on the belt. They were impressed and wanted to see what Flexco could do for them. When Larry called the specs into the product team, we recognized that the 130” (3.3m) belt was almost twice as large as the largest cleaner available. But the solution was easy – we simply extended the pole and fitted it with two of our 60” blades. And now we have a happy customer with clean belts.
Mission Impossible (Or Is It?)
And once in a great while, there are the projects that seem like they are impossible. That is, until we all get in a room and put our heads together to come up with a solution. This was the case with a challenging application that Territory Manager Matt Thomsen brought to the table. Let’s just say the end result was a labor of love, but it is always good to see something go from paper to install, to success.
Matt was at a facility that was moving taconite when they told him that they were having problems keeping a cleaner on top of the cone crusher. Because of the abrasive nature of the taconite, cone crusher parts were being replaced every six to eight weeks. In order to replace them, the chute that the cleaner fits into had to be disassembled. When the chute hood was removed, it would hit the cleaner, bending it and making it unusable. So along with replacing cone crusher parts, they were cutting out the cleaner and replacing it.
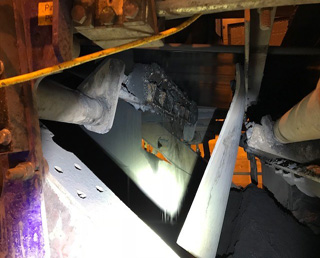 |
There are three retractable MHS cleaners at this quarry now, with more to come. |
Several drawings later, Sr. Development Engineer Joe Snow had a retractable MHS Secondary Belt Cleaner designed and ready for install. The threaded rod on top of the tensioner first pushes the blade away from the cleaner, allowing the maintenance team to slide the cleaner out of the way while they get the hood off and replace the cone crusher parts. Once the hood is replaced, the cleaner slides back, and the tension is relieved from the top threaded bolt to bring the cleaner blade back to the belt.
Matt and the product team worked with his customer to find a solution because that is what we do here at Flexco. We walk the path with you, and we both learn a few things along the way. We find out what works and what doesn’t work for our customer and we have a willingness to do whatever it takes to make our customers’ lives easier.
So if you encounter an application that stumps you, pick up the phone and give us a call, shoot us an email, or hit the chat button on the Web site. We’ll be happy to face your challenge head-on and come up with a solution. If you aren’t sure what you need, a belt conveyor assessment is always a good way to begin. We’ll have one of our experts come out to walk your conveyor and offer suggestions to improve your productivity. And then maybe your application will end up right here, in a future blog.
Authored by: Kevin Fales, Product Manager
Fales manages the belt conveyor product (BCP) line, providing product development and engineering with guidance on market requirements for both new product concepts and existing products. He also leads the development of technical and promotional literature supporting BCP line. Fales graduated from Grand Valley State University with a bachelor’s degree in Marketing, and from Western Michigan University with a Master of Business Administration.