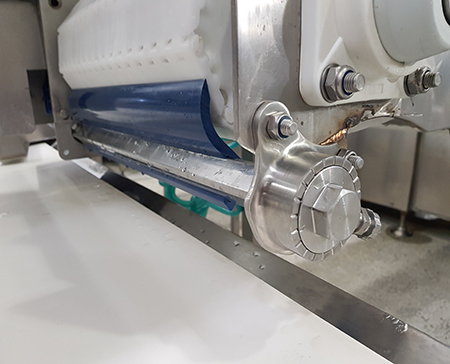
Industry
Food Processing
Application
Lamb Processing Facility
Product
FGP Food Grade Precleaner
Objective
Eliminate carryback
Reduce downtime
Speed maintenance
Conveyor Detail
Modular and white nitrile plied belts
Problem:
A lamb processing facility in New Zealand was experiencing severe carryback on a conveyor in its lamb processing room. The conveyor was seeing over 44 lbs (20kg) of carryback per day, which affected both its product output and the bottom line of the company. Two modular belts in the lamb cut room experienced the most carryback and presented serious challenges for the site.
Solution:
The meat processing company originally had a cleaner which consisted of segmented blades mounted onto a head pole. This cleaner was then mounted onto the head pulley with the blades tensioned via a counterweight system. But poor design meant meat would accumulate between the cleaner tips and the belt’s surface, causing enough tension to flip the cleaner over and render it useless. Production had to be stopped three to four times per hour for blade cleaning because the counterweight system was hard to tension. The excessive carryback also caused good cuts of meat to fall to the floor, making them unfit for human consumption and costing the company hundreds of dollars per week. Upon seeing the design of the FGP Food Grade Precleaner from Flexco, the company decided to take a chance on the stainless steel model, complete with a FDA-approved, metal detectable blade.
Result:
Installation of the FGP instantly salvaged up to 44 lbs (20kg) of lamb per day, adding to stock levels and reducing waste. The FGP cleaner also eliminated the need for the system to be constantly cleaned and maintained because of the easy tensioning system minimized blade wear and maximized the cleaning efficiency. By eliminating the need for constant maintenance, the company saved more than $1,700 USD ($2,500 NZD) per year in labor. Apart from monetary savings in wages for the excess labor previously required, the company also gained time and increased productivity as the maintenance crew was now free to perform other productivity-boosting tasks instead of constantly reacting to the same problem.